WORKMASTER® Electric Motor Starters feature best-in-class components, superior construction, and ease of installation. These units minimize motor failures, nuisance tripping, and plant downtime.
WORKMASTER® Motor Starters combine the best of these various elements: NEMA rated enclosures, best-in-class contactors, solid-state overloads, rugged switch bodies with gold-flashed contacts, together with careful, rugged construction, and wire-labeling, all recorded on easy-to-follow schematics to provide the best means of controlling and protecting the “muscle” that powers your plant operations, and keep production flowing. We offer a standard line of full-voltage Starters, which are manually (pushbutton) operated, and also a line of externally activated Starters, which are designed to be interlocked with nearby equipment.
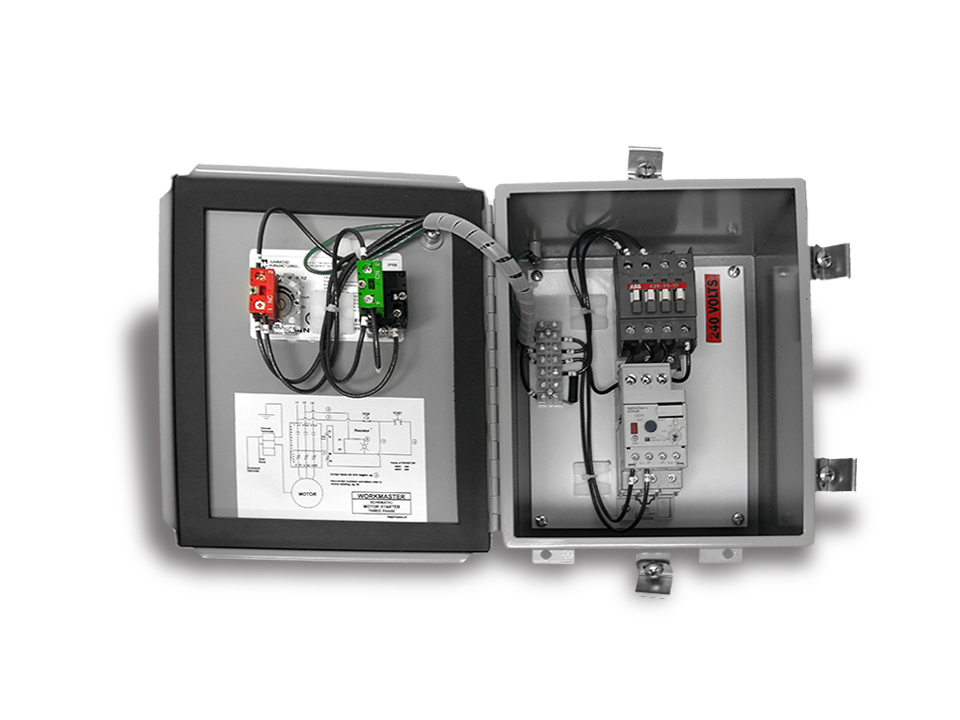
Motor Starter Elements
Contactors
Overloads
Solid State Overloads
Pushbuttons, Switches & Pilot Lights
Industrial operating conditions are often challenging to manually operated controls. A combination of rugged mechanical design and anti-corrosive switch contact material is ideal. Corroded contacts in switches interfere with operation of a motor and also cause intermittent momentary contact–so-called “relay chatter”. When a motor is subjected to this erratic form of powering, the possibility of motor damage greatly increases. To address these issues, WORKMASTER® uses a line of industrial pushbuttons and switches that feature NEMA 4 / IP65 ratings and metal switch bases (which are automatically bonded to the enclosure) are equipped with contact blocks with gold-flashed contacts.
Illuminable Pushbutton
LED Light Module with Bonding Screws
3-Position Operator
The illuminated versions of these switches or pilot lights use LED illumination, which is the most reliable form of illumination available, lasting far longer than incandescent or neon illumination, while consuming less power. Using LEDS, the likelihood of pilot light burnout is virtually eliminated.
POWER SOURCE | FLA RANGE OF OVERLOAD (AMPS) | MOTOR HORSEPOWER (HP) | NEMA CONTACTOR SIZE | STANDARD MOTOR STARTER | DUAL MOTOR STARTER* | DOUBLE MOTOR STARTER** |
---|---|---|---|---|---|---|
Single-Phase 120V | 1.00 - 5.00 | 1/4 | 00 | 29-20020 | 29-20021 | 29-20022 |
3.20 - 16.00 | 3/4 | 0 | 29-20030 | 29-20031 | 29-20032 | |
Three-Phase 240V | 0.20 - 1.00 | 1/4 | 00 | 29-20040 | 29-20041 | 29-20042 |
1.00 - 5.00 | 1 | 00 | 29-20050 | 29-20051 | 29-20052 | |
3.20 - 16.00 | 3 | 0 | 29-20070 | 29-20071 | 29-20072 | |
Three-Phase 480V | 0.20 - 1.00 | 1/2 | 00 | 29-20045 | 29-20046 | 29-20047 |
1.00 - 5.00 | 2 | 00 | 29-20055 | 29-20056 | 29-20057 | |
3.20 - 16.00 | 3 | 0 | 29-20075 | 29-20076 | 29-20077 |